Home » Positive Drive
Positive Drive
The two most common mechanical problems that occur running conventional flat belts are Slippage and Off-Tracking. Slippage is the loss of frictional contact on the drive due to moisture, fluids or load. Off-Tracking occurs where the load carried is not evenly distributed across the width of the belt resulting in the belt being pushed to one side.
Volta’s Positive Drive belts have been engineered to utilize two positive drive designs to overcome these main problems. The two designs of drive teeth are engineered to give various drive effects for different applications and uses. They are available in a wide range of choices.
Material Features
Varying drive tooth pitches
Profiled and textured top and bottom surfaces
Various Thicknesses
Food and non-food grade options
Cold & heat resistance capabilities
Non-absorbing, hydrolytic resistance
Metal detectable materials
Volta`s Positive Drive Belts
This range has evolved over nearly two decades, guiding companies in food production and the engineering companies that manufacture conveyors, to an improved more hygienic way of conveying products and building systems. The food grade versions form the backbone of many food processing facilities across the globe and combine mechanical and hygienic excellence in one streamlined product. The massive install-base we have accomplished across all sectors of food processing and our dedication to developing top quality thermoplastic belting material has enriched Volta’s in-house knowledge and given us an unparalleled ability to design and customize solutions without compromise.
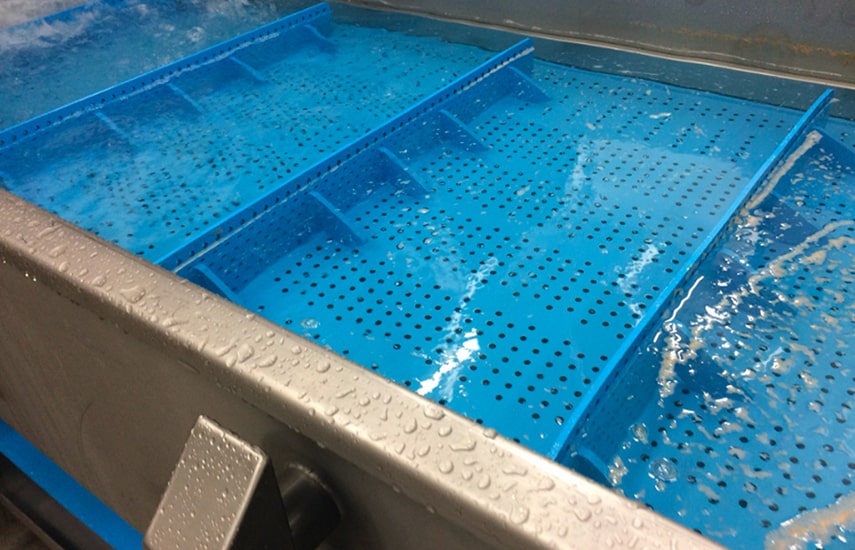
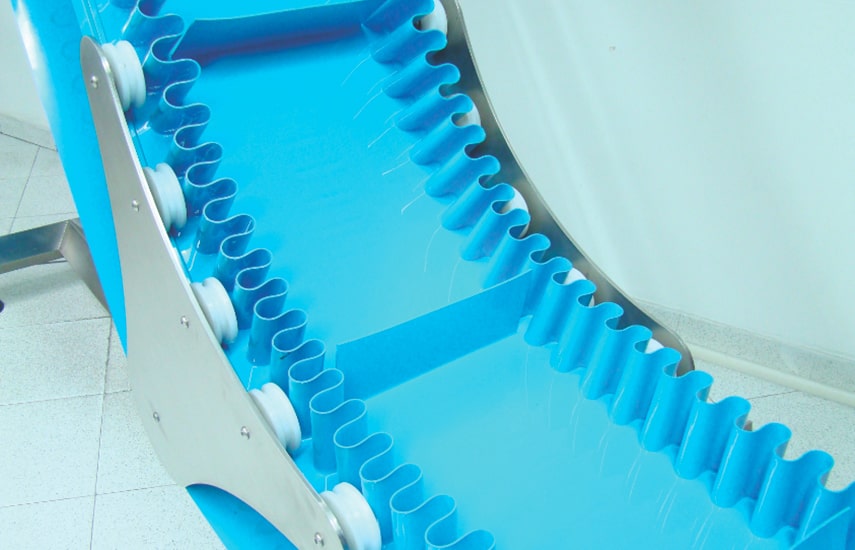
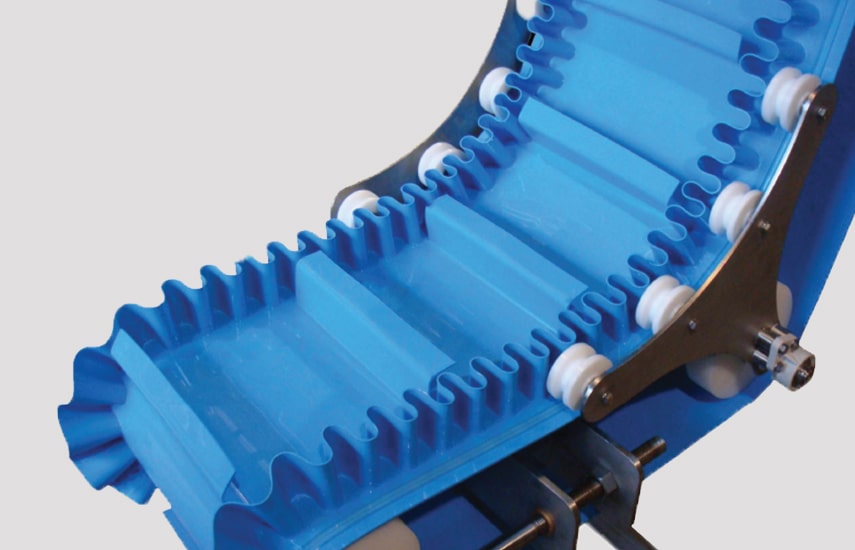
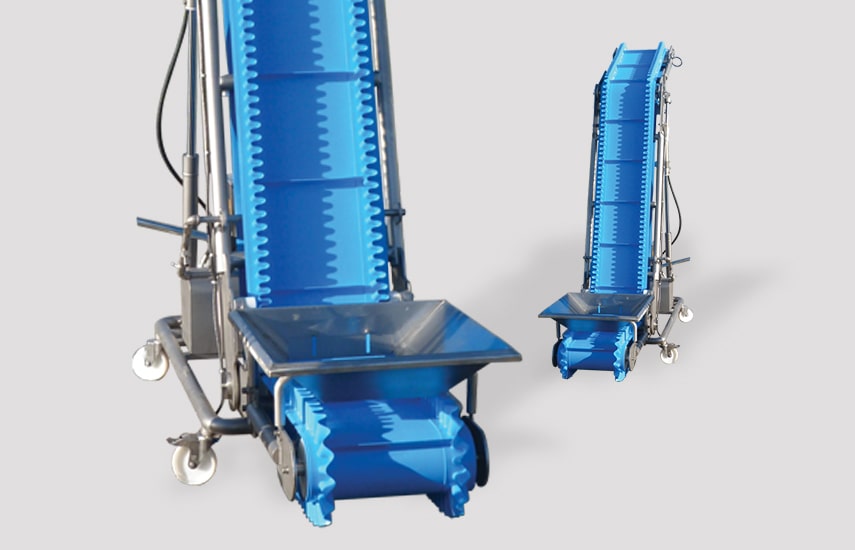
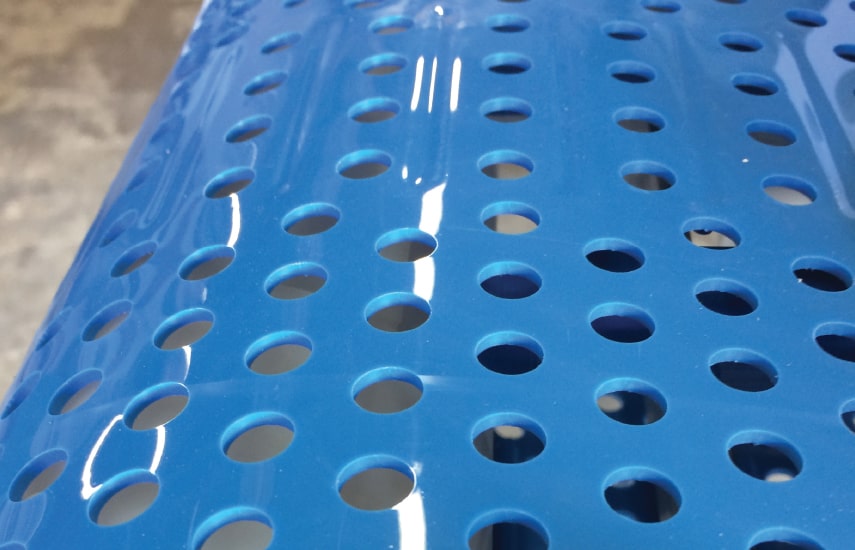
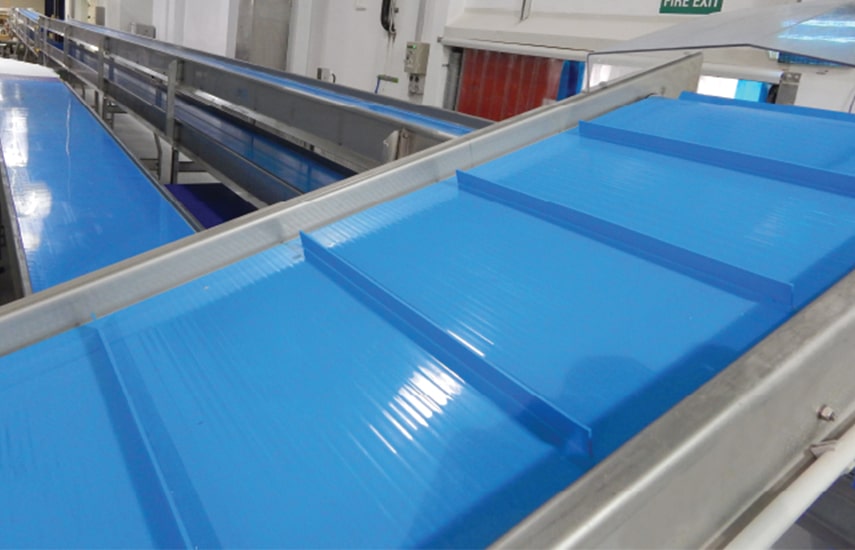
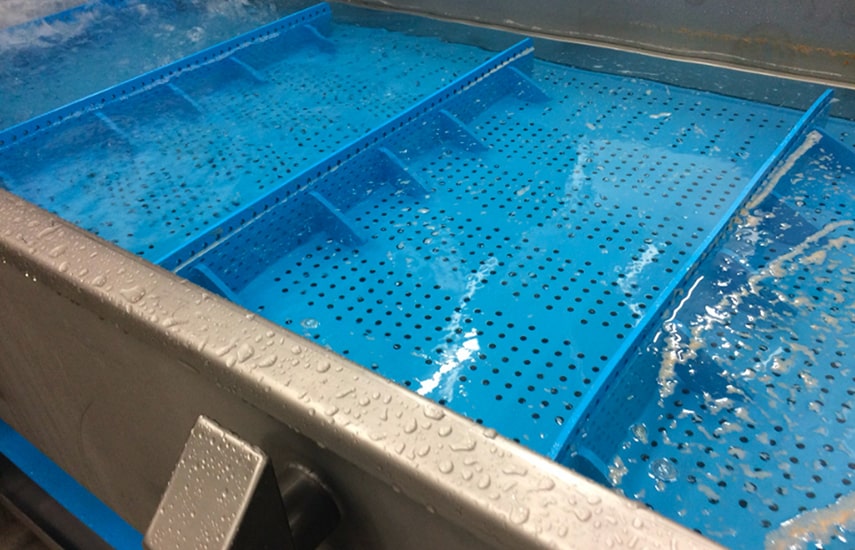
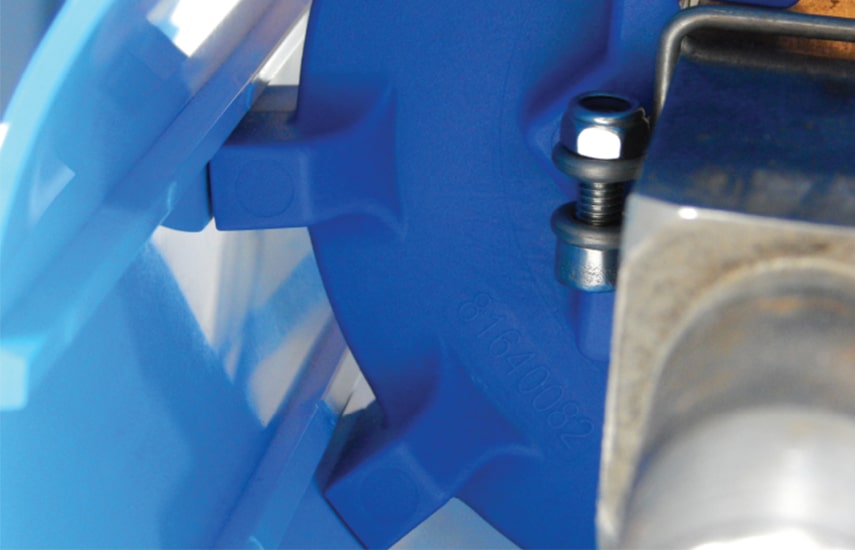
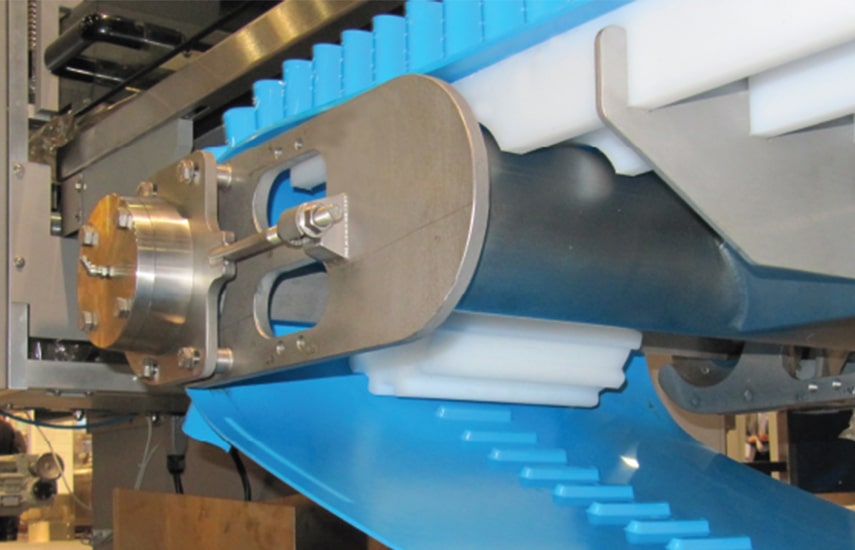
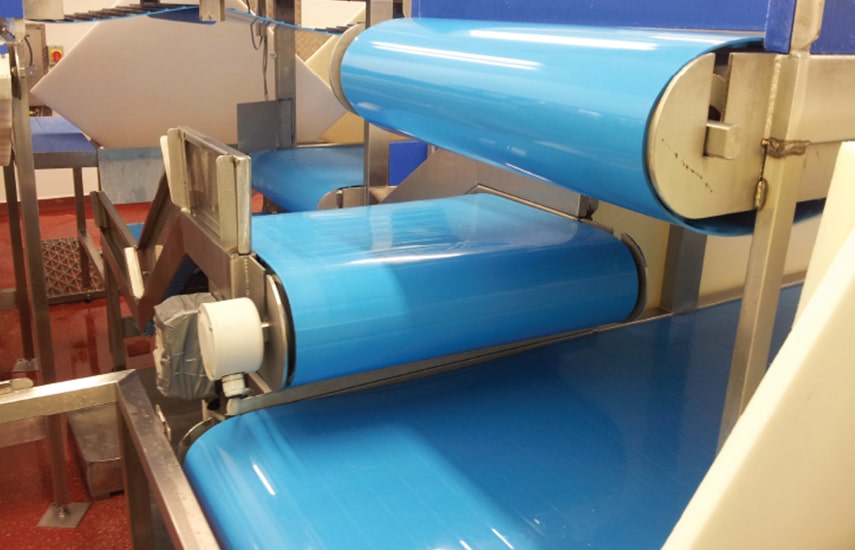
Widest Range of Positive Drive Belts
The chief designs Volta developed are based on lateral teeth (called DualDrive™) that run the entire belt width and a central tooth design based on one or more rows of teeth (called SuperDrive™). Since 2002, these Volta products have become an indispensable element in the hygienic design of food processing plants as well as providing smart solutions for heavy non-food products, where operating conditions causing heavy wear and tear, off-tracking, and slippage are unacceptable. The entire range can be fabricated to equip elevator/ Z-or swan-necks and other conveyor types. Welding fixtures for splicing these belts on site are available in convenient sizes.
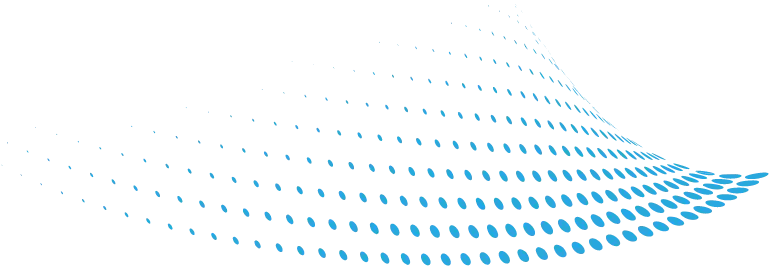
We are Your Partner
Volta offers an unparalleled degree of flexibility in construction of these belts for conveyor design with a technical support that is the envy of the industry. Over the years, we have developed a particular aptitude for project work and our trained staff can assist with optimizing belt design to reduce the cost of investment and enable the end user to benefit fully from our technological offering. We actively share our expertise with our long-term partners in the industry and support them with a personal and individualized touch.
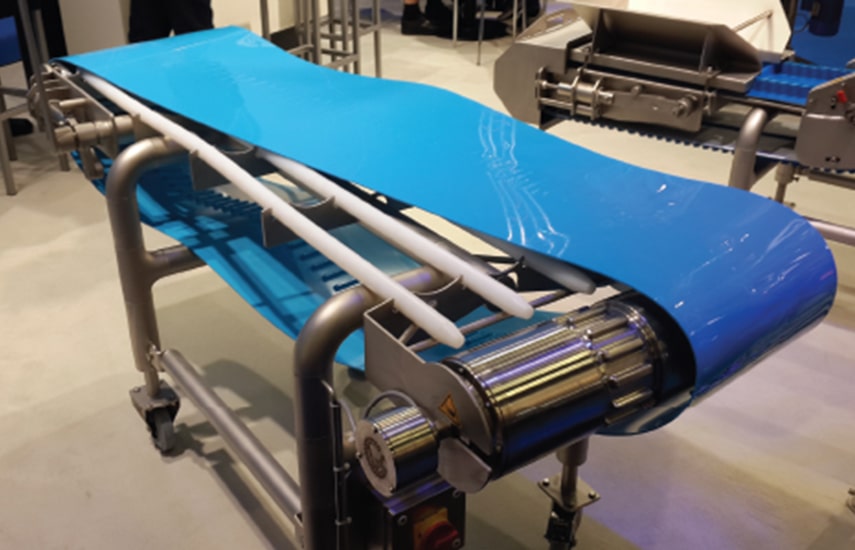
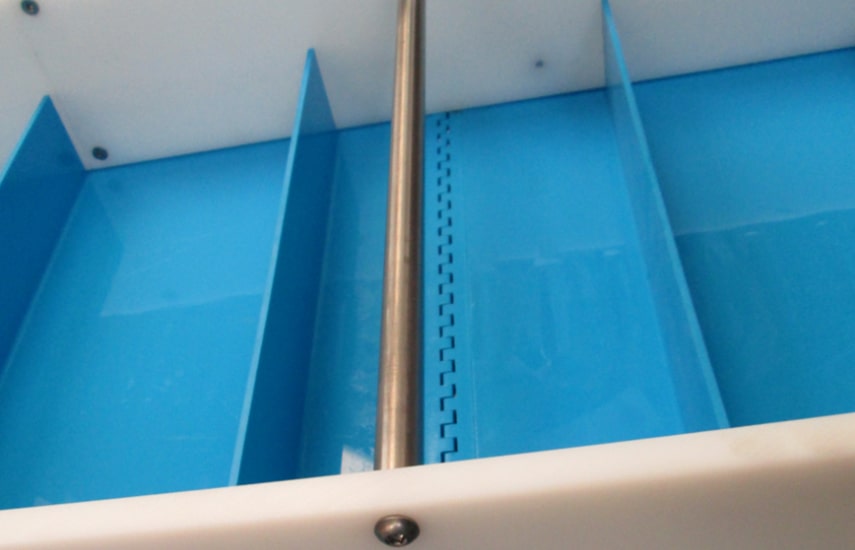
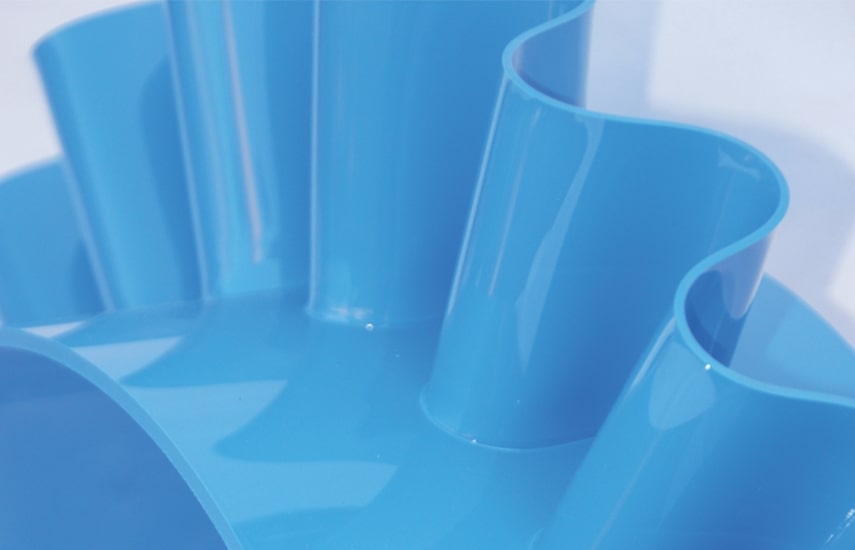
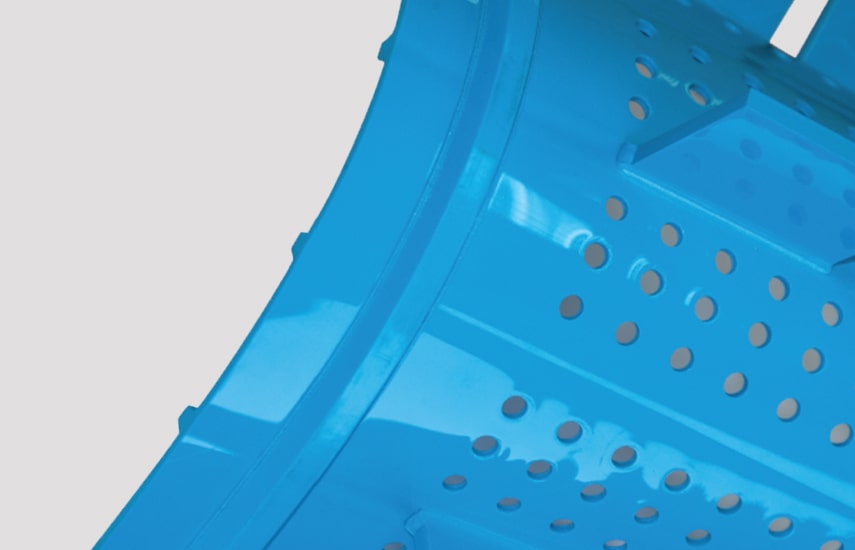
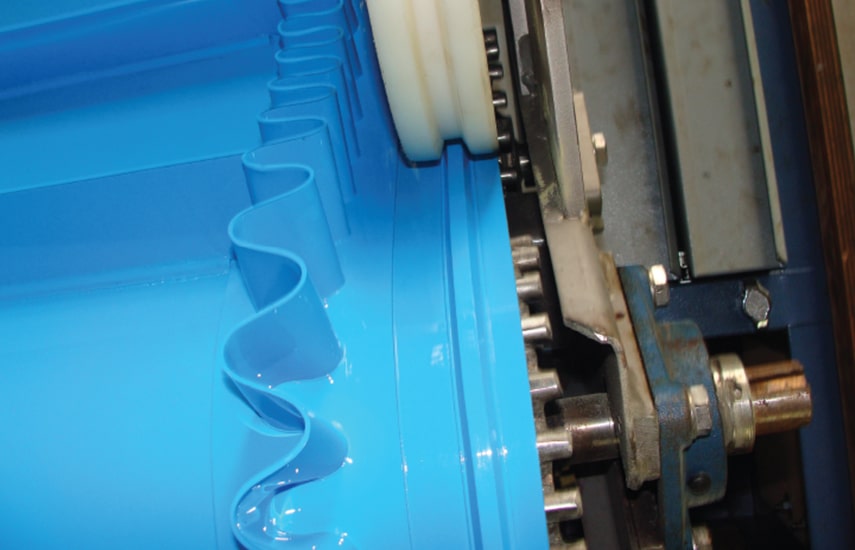
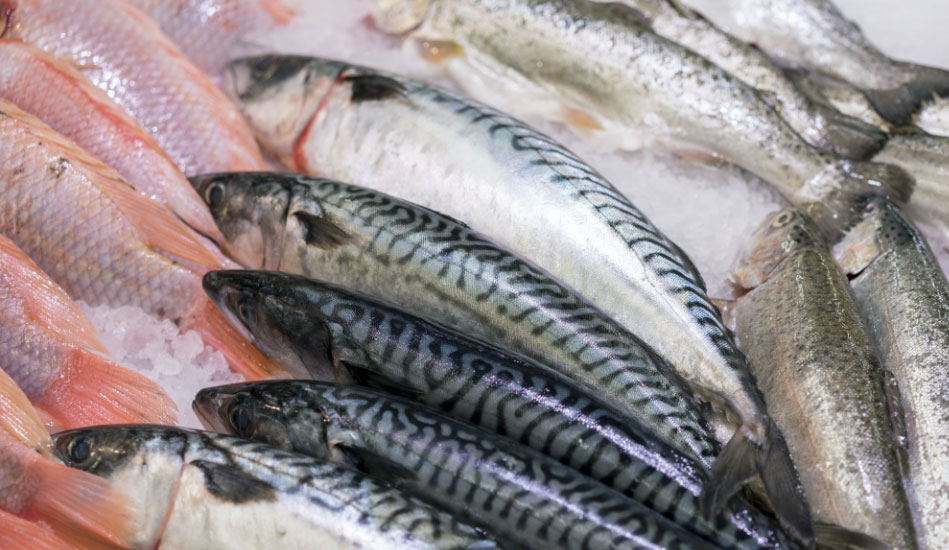
Mr.Van de Deijl, Interfish, IJmuiden
Conveyors
Are you looking for a solution?
Learn from our experience
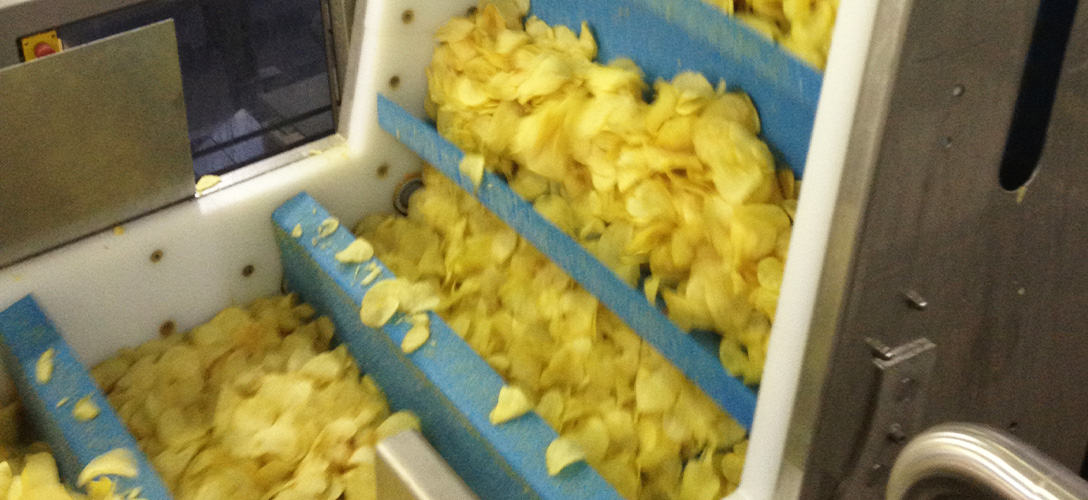
The snack food market is a global market. The main consumers reside in Europe and North America.
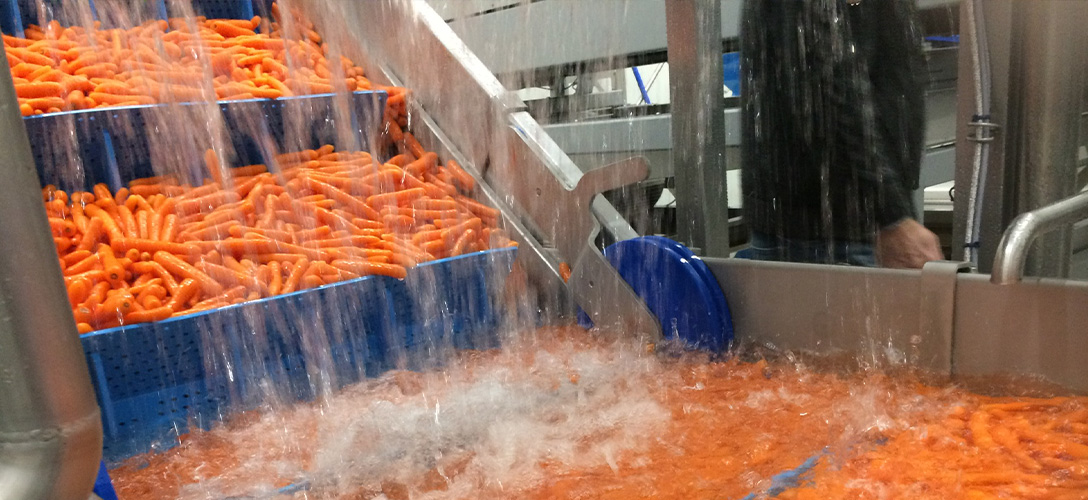
Washing operations for vegetable processing plants begin with intake belts washing off field soil and continue with washing/rinsing prior to and after peeling.
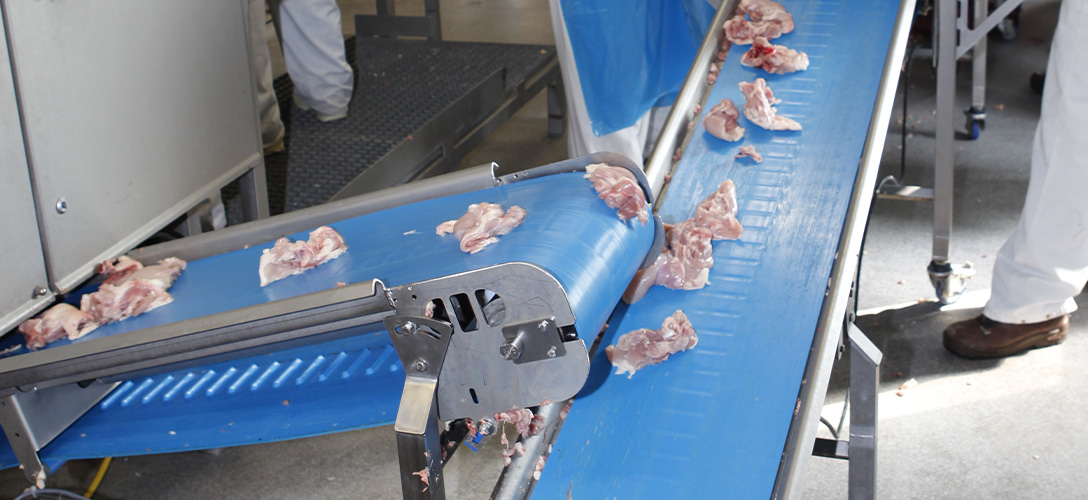
Holland is an important producer and exporter of processed poultry. The techniques for raising the birds have been honed to perfection and naturally, this striving for excellence has filtered through to the processors.
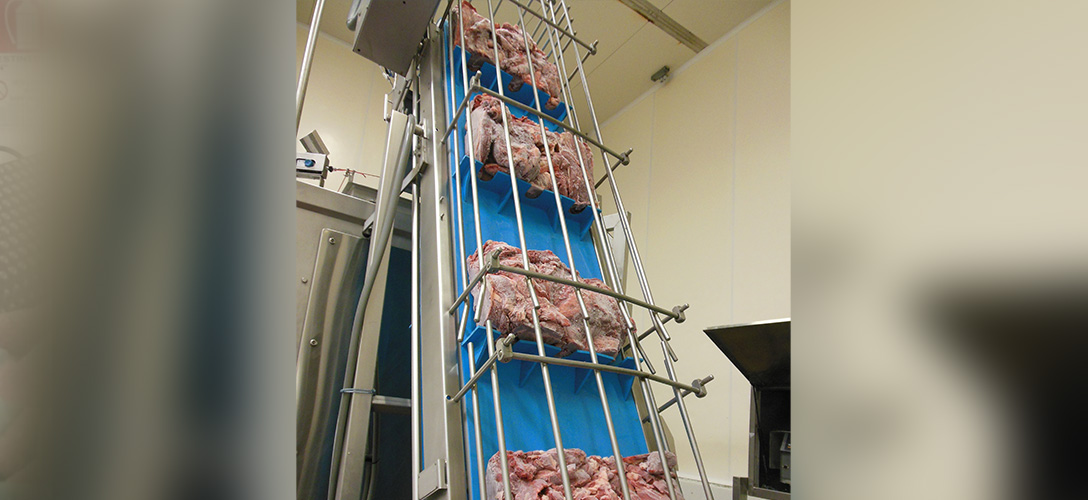
A well-known producer and seller of meat patties used modular belts for the elevation of 25kg frozen blocks into a grinder at an angle of about 85 degrees. The loading is manual and relies on workers paying close attention to the exact position of the moving belt.