The stamping room in a leading international automotive plant that monitors all their production with a Kaizen system, took steps to improve productivity in the press conveyors used to stamp car doors. With a car rolling off the line every couple of minutes, even the breakdown of a three-ply fabric belt once in 6-8 months is a burden. Volta supplied a 3mm thermoplastic belt for this long, 1600mm wide conveyor. The manufacturers saved 4 hours of production time on the initial installation using a Volta FBW welding tool to join the belt on the conveyor. After one month operator error resulted in a door panel cutting into the surface tearing the centre of the belt. The works manager assumed from his experience with traditional plied belt, that the Volta belt would need to be thrown out. To his amazement, our local team went on site and welded the tear closed, using our thermoplastic electrode making a virtually invisible repair. The belt lasted an additional two and a half years, saving the company three costly changeovers and giving an estimated saving of twenty thousand dollars in production down time for that period.
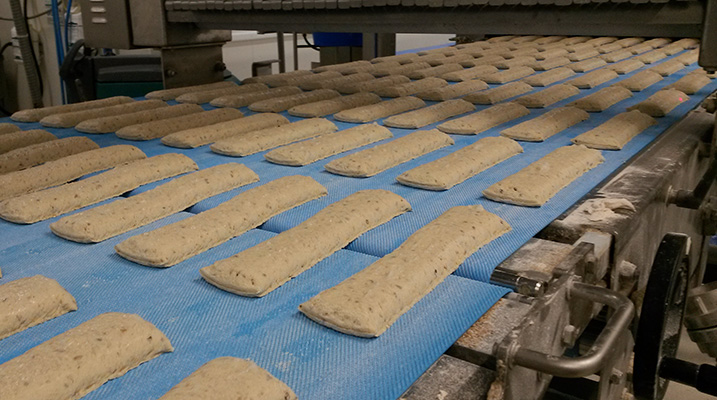
Volta Belts in Crackers & Bagels Production
The maintenance manager says: “Although a Volta belt is more expensive than the plied belt, at the end it turns out cheaper – because the cheap turned out to be expensive for us!”