Home » Industries » Food & Hygiene » Poultry
Poultry
Poultry is considered the most sensitive food stuff in terms of pathogenic contamination and is a significant part of people’s dietary intake in many countries worldwide. Hygiene in poultry processing can come at a cost with auditing standards demanding frequent washdowns and disinfections. Our product consistently tests with lower bacteria levels than conventional belts. The reduction of water usage and manpower required to service, provides major savings. It has an environmental impact as well, reducing water treatment costs, making Volta thermoplastic conveyor belts a safe and economic choice. We supply full slaughterhouse lines and our belts handle blood, viscera, feathers, and processed meat including breadcrumbed and frozen.
Poultry processing in The Netherlands
Holland is an important producer and exporter of processed poultry. The techniques for raising the birds have been honed to perfection and naturally, this striving for excellence has filtered through to the processors. Over 60 conveyors with drum motors were converted from modular belting to Volta SuperDrive™ including waste conveyors where the guiding principle was the prevention of cross contamination. This occurs between conveyors in the same processing hall either from accidental movement of workers between stations or from negligent spraying water during cleaning. The superior hygienic nature of Volta’s thermoplastic belting reduces the risk of cross contamination of the belts and reduces the amount of water used during cleaning.
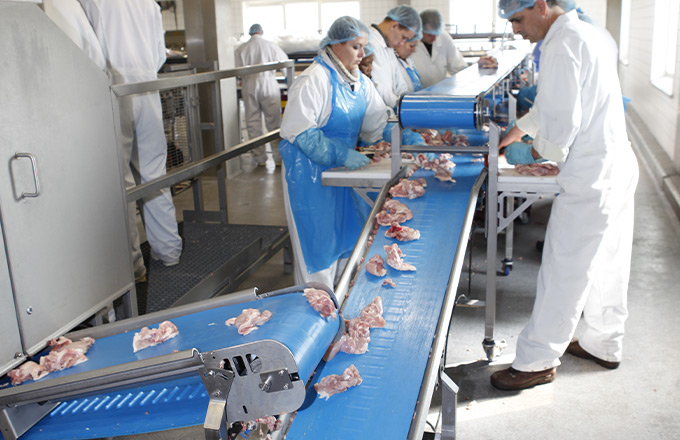
Sausage/smallgoods manufacturer
A leading European producer of poultry sausages and smallgoods uses Volta extensively on over 50 conveyors. The product conveyed is soft and the OEM is a long-term Volta partner. Only wear and tear can result from accidents or over-cleaning. In fact, there has been minimal damage and many of the belts have given over 6 years of hygienic service. The variety of conveyors include; horizontal conveyors, inclined troughs, cleated belts and a sausage transfer machine with multiple lanes equipped with 65mm wide flat V profiles. The factory has reduced their cleaning time and cost significantly. They also enjoy improved swab test resulting in extended product shelf life all since abandoning modular and plied belting.
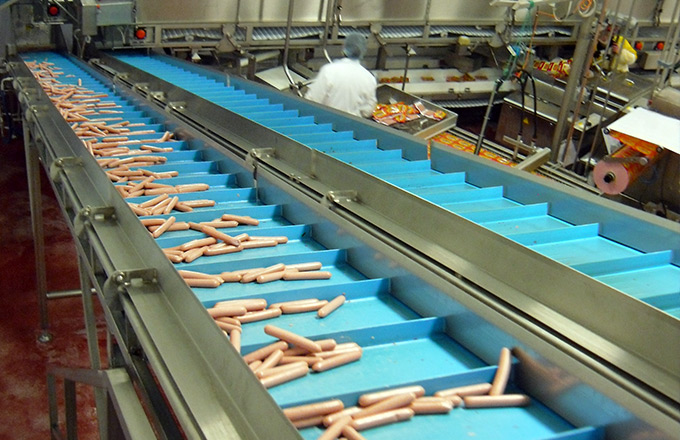
Turkey processing
A large turkey processor made a side-by-side comparison of Volta SuperDrive™ and conventional modular belt. The plant has installed an increasing number of both Mini SuperDrive™ and SuperDrive™ belts as the advantages of the thermoplastic belting became clear:
- reduced cleaning time
- significant overall savings in the cost of ownership
- quieter working environment
- a cleaner, safer product.
The Mini SuperDrive™ was selected where existing sprocket diameters were below 100mm with the heavier operations being taken on by the SuperDrive™.
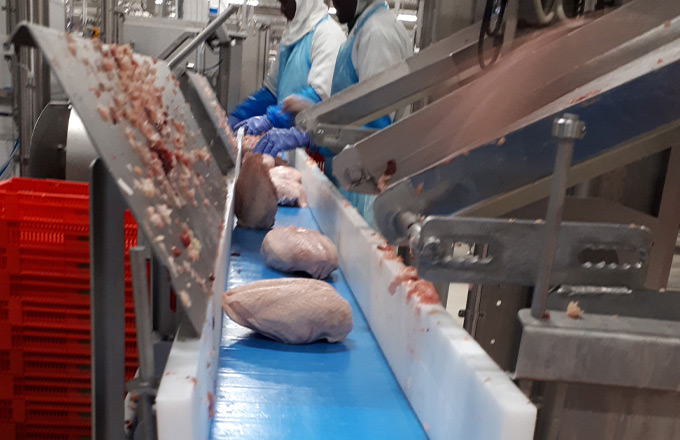