In the last decade, the recycling industry moved from an afterthought industry to a major production. As the recycling industry matures by adding more materials to recycle, the production plants need to adopt their operational equipment and systems to match these materials.
The expansion of recycled materials brought familiar production challenges that many other industries were already facing, such as high energy consumption, safety, and health conditions. Many experts in the industry started to question whether the recycling plants were meeting the benefits of recycling these materials or just creating new environmental and health issues. It would be absurd if the recycling industry did not do its utmost to take care of its own working environment.
As recycling plants need to operate the conveying, sorting, handling, and cleaning, while dealing with different sizes, weights, and substances, the focus of maintaining effective solutions to transfer these materials became paramount.
Therefore, the belts and the conveying systems should be assessed as to whether they need to be upgraded to manage the concerns of the recycling industry’s production plants. Fast forward to the present and we are looking at the next generation of belting solutions. Here are just a few reasons why recycling plants should consider switching over to thermoplastic belts.
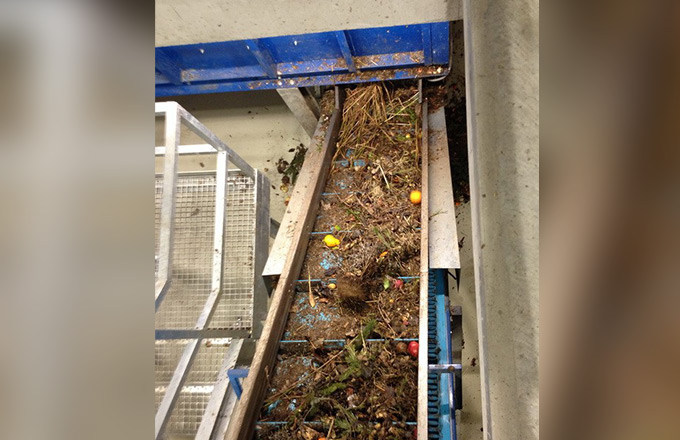
Managing New Materials
The recycling industry has moved past just paper and plastic. Today, recycling plants are expected to handle a much wider variety of materials. For example:
- Batteries
- Biomass
- Electronics
- Glass
- Metal
- Paper
- Plastic
- Wood
Each one of these materials poses operational challenges at each stage of the process, regardless of whether the production plants are dealing with industrial or household, sorted or mixed, and whether used on conventional conveyor types or on magnetic systems, such as Eddy Current separators.
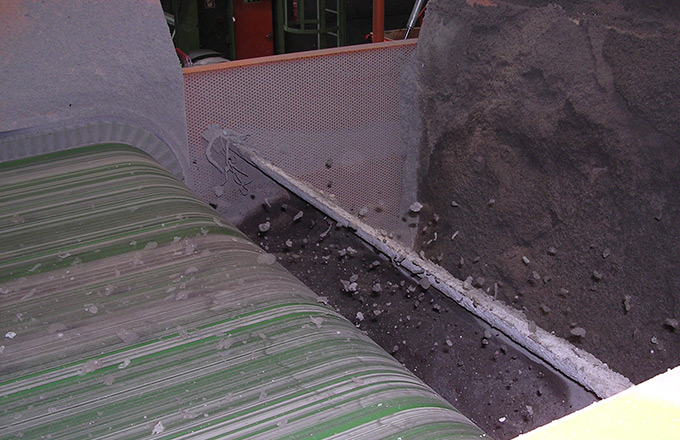
Common recycling processing issues include:
- Transferring solid waste in unbroken large pieces, granular, or in powder form.
- Sorting lines where manual sorting is incorporated, or high-speed belts are used with optical sorters.
- Magnetic conveyor systems with magnetic drums, over band conveyors and Eddy Current separators
- Rubber belts that are heterogeneous can leave particles in the air and require mask wearing for employees.
In order to deal with all these types of materials and processes, the belts being used should be made of a homogeneous material that can handle them, specifically thermoplastic.
Made to Last
One of the most common issues that recycling plants deal with on a regular basis is the constant need to replace or repair by removing them from the facility. This can cause an economic burden due to the production downtime while the issue is dealt with by the team.
Therefore, the maintenance of the belts becomes the operational team’s primary concern. The maintenance process and related cost of the belt is measured by its durability. Thermoplastic solutions can absorb the vibrations based on weight and speed, which directly affects the joints. The belts can be fixed and replaced without removing it from the production line or the facility, significantly reducing the downtime related resulting in a reduction of production interruptions.
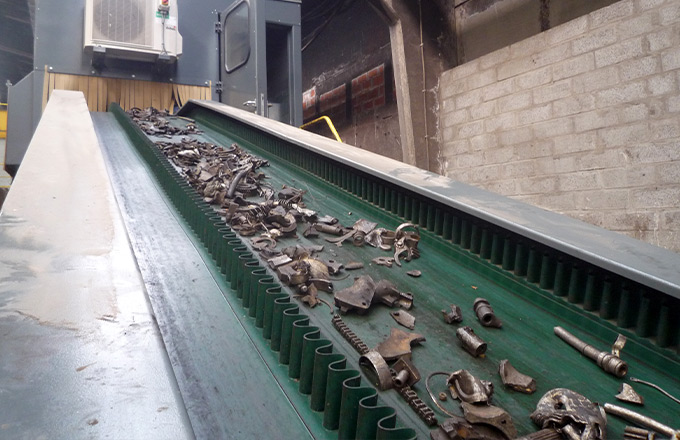
Cost and Production Efficiency
The same solutions that improve production efficiency also reduce production costs with thermoplastic belts.
There are 2 major advantages through thermoplastic belts.
- The material has a high impact resistance to chemicals, oils, abrasions, and cuts which makes the belts durable. Therefore, spending on repairs and replacements is significantly reduced.
- Fast and easy on-site assembly and replacement leads to a reduction in production downtime.
Boost Productivity
Using thermoplastic belt solutions for recycling production plants accomplishes everything the industry set out to do. They are able to handle a wide range of materials, and are capable of handling each stage of the recycling process. They are extremely durable with a high resistance to abrasions and absorb vibrations. Finally, they increase profitability due reduced downtime as the maintenance can be completed on site.