Home » Positive Drive » Mini DualDrive™ (MDD)
Mini DualDrive™
Mini DualDrive™ (MDD) is a 1” pitch Positive Drive belt. The homogenous structure works smoothly and silently with minimal strain, thereby extending belt life and saving wear and tear on bearings and other conveyor components. The full width teeth give extra lateral rigidity to the belt and makes it suited to applications where this is a critical factor or design requirement. For example: Narrow conveyors with no central slide bed support, combined with a small pulley diameter.
Material Features
Rigid lateral design
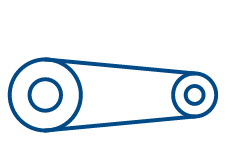
Used on pulley sizes from 48mm and up
Recommended for tight transfers with center drive
Fabrication and perforation options available
Budget retrofitting from 1” pitch modular systems
Advantages
Mini DualDrive™ is manufactured from high performance, food grade TPE/TPU materials and is also suited to replacing 1” pitch modular belts with a minimum of retrofitting. Its ease of installing as a conveyor belt replacement can be seen in one of the case studies on this website and it is a value-added food grade conveyor belt for processors seeking to reduce the cost of ownership. It can be used wherever there is direct contact with food in all its stages of production to reduce the potential for contamination.
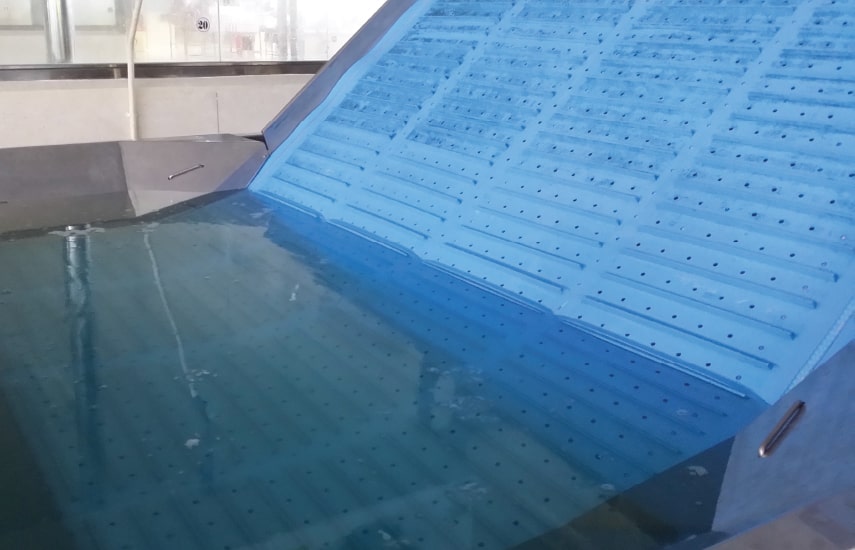
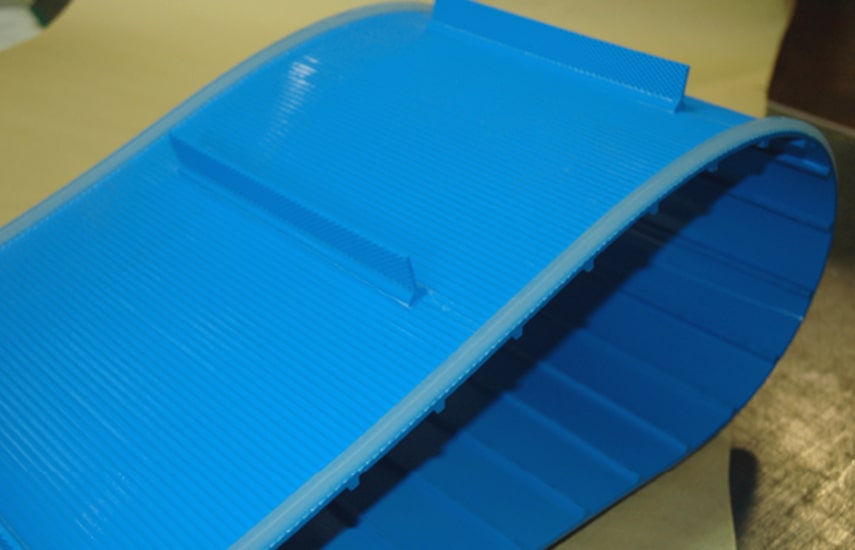
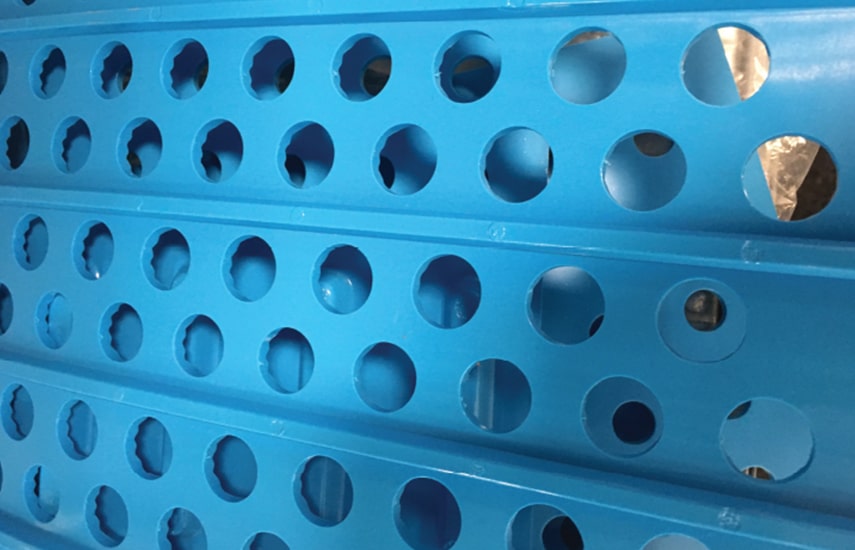

Hygienic Solution
The demand for food grade belts has led to a huge variety of belt types in the marketplace, making the choice difficult for a processor who has specific requirements and must work efficiently and on budget. Guidelines are emerging which often find it easier to describe what is not hygienic but there is agreement that homogenous belts are the most hygienic conveyor belt option. For companies unwilling to invest in new conveyors, the conversion from old modular technologies to hygienic thermoplastic belting can be done on a convenient limited budget with Mini DualDrive™.
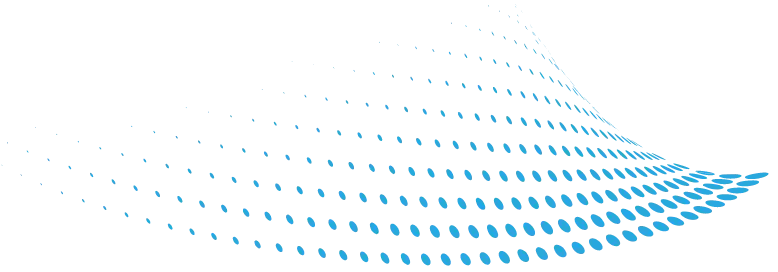
Conveyors
Are you looking for a solution?
Learn from our experience
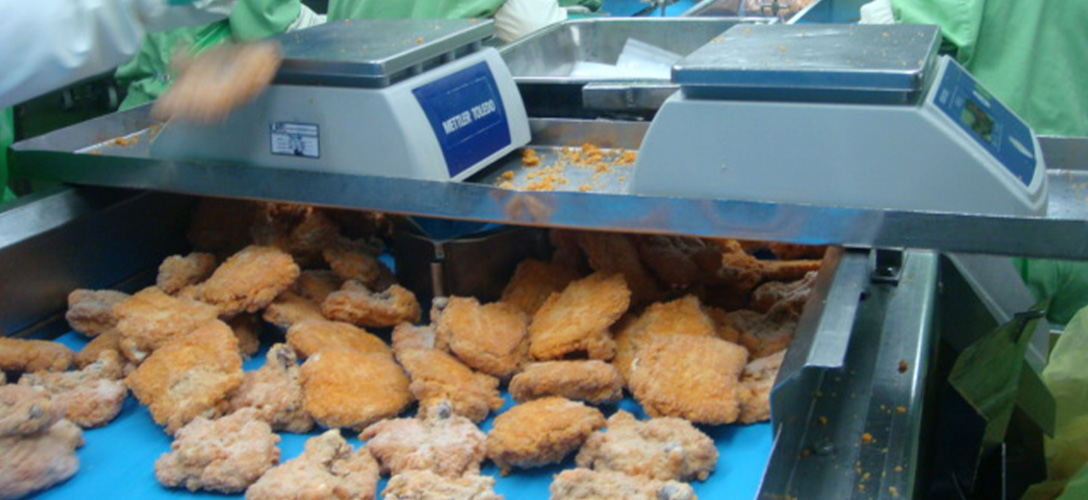
Fish and seafood can present belt suppliers with some of the most difficult challenges in food processing.
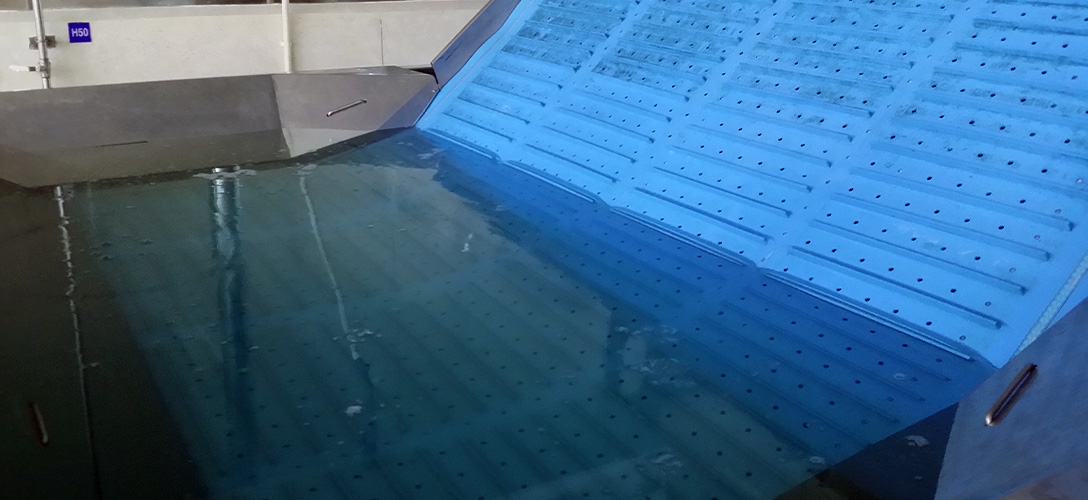
Shrimps and prawns form the backbone of several developing economies and factory processing…
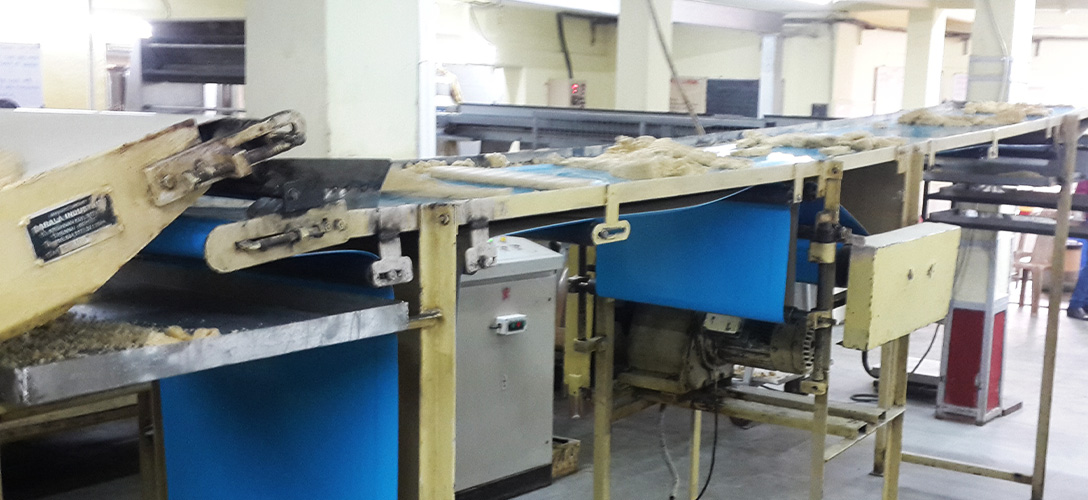
One of the world’s largest producers of cookies used conventional plied and canvas belts for decades. They were required to change them every two to three months because the splice failed on the finger joints from following a belt path that included nine pulleys.
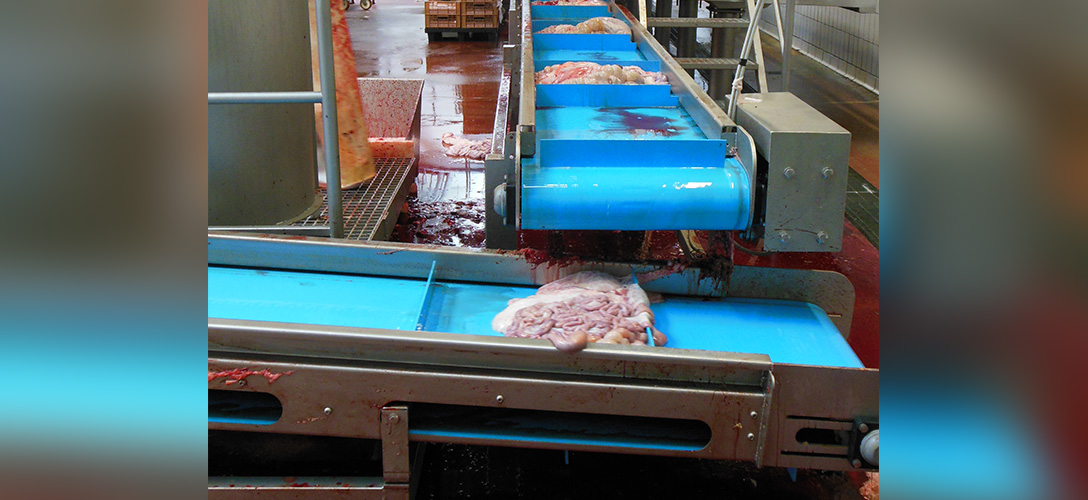
A newly equipped pork abattoir commissioned a set of conveyors designed with two flat belts that transferred offal at 90 degrees on a corner. The belts used synchronized compartments comprising of full width cleats, to keep each set of organs separate until the veterinary service on site had confirmed the meat as fit for consumption.