Bottling plants and bottle producers must deal with the rejected material that has chips and cracks which might injure customers when the product is used. Bottling operations are typically highly automated and bottles are conveyed upright along S bends and other diverters which make the factory layout complex and difficult to access for maintenance during working hours. A major producer of soft drinks installed five long reject lines conveying bottles from under the machinery and out of the building to totes for recycling. Each three-ply PVC belt lasted around 8 months which meant a shutdown every 6 weeks on average, causing production loss. A Volta belt with a homogeneous dense top layer but thinner than the original ply belt, gave 5 years of service and saved maintenance costs and increased productivity.
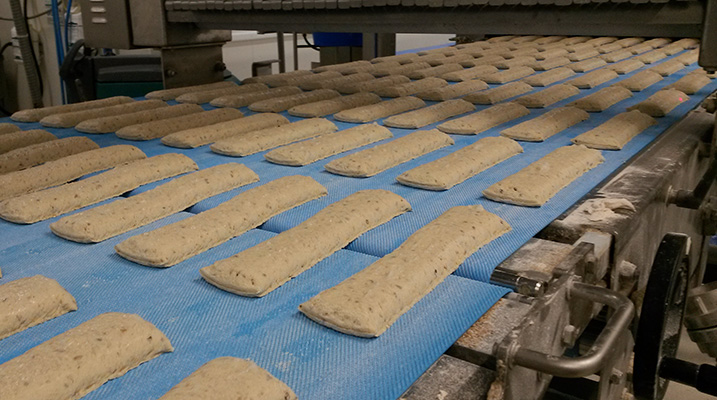
Volta Belts in Crackers & Bagels Production
The maintenance manager says: “Although a Volta belt is more expensive than the plied belt, at the end it turns out cheaper – because the cheap turned out to be expensive for us!”