TRANG CHỦ » Industries » Industrial Applications » Automotive
Automotive
The solutions we have developed with our partners are built on decades of accumulated knowledge with thermoplastics. Many manufacturers understand that conveying systems can be an economic burden on the cost of ownership. Frequent belt changes and the resulting costly down time coupled with the increasing service costs and difficulties of bringing outside contractors on site, are all reasons to consider a different, more economical approach.
Automated assembly plant
Volta accepted a challenge of developing a narrow composite belt that carries car chassis through an assembly line, past consecutive workstations. Belts were designed for a system 25 metres between axles and 55mm wide. These belts transport loads in excess of 4 tons (10500 lbs). Wider belts enable even heavier loads to be carried.
The belts do not elongate and have no joint. They are wear and paint-resistant, making them the perfect choice for an industrial setting where break downs would require a prolonged and expensive shutdown. With the old-style belt, partly assembled cars would be required to be removed during the changeover. The cars would have to be replaced on the line costing extending down time before they could continue production.
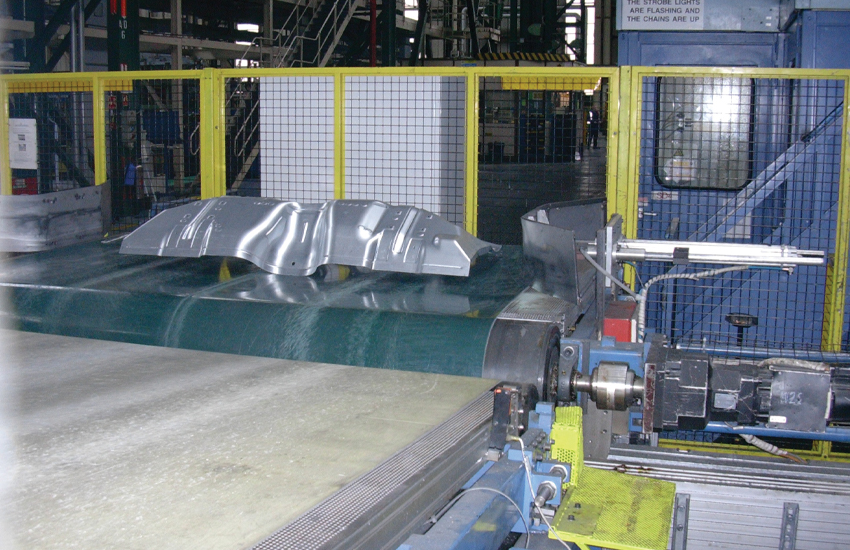
Stamping lines
The stamping room in a leading international automotive plant that monitors all their production with a Kaizen system, took steps to improve productivity in the press conveyors used to stamp car doors. With a car rolling off the line every couple of minutes, even the breakdown of a three-ply fabric belt once in 6-8 months is a burden. Volta supplied a 3mm thermoplastic belt for this long, 1600mm wide conveyor. The manufacturers saved 4 hours of production time on the initial installation using a Volta FBW welding tool to join the belt on the conveyor. After one month operator error resulted in a door panel cutting into the surface tearing the centre of the belt. The works manager assumed from his experience with traditional plied belt, that the Volta belt would need to be thrown out. To his amazement, our local team went on site and welded the tear closed, using our thermoplastic electrode making a virtually invisible repair. The belt lasted an additional two and a half years, saving the company three costly changeovers and giving an estimated saving of twenty thousand dollars in production down time for that period.
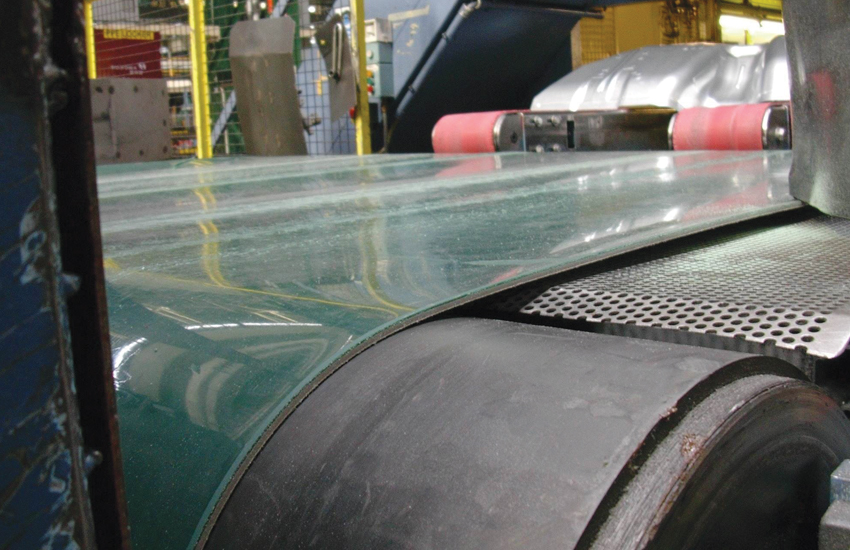
Painting room
Automotive paint rooms need to be completely dust-free. The smallest particles can stick to the bodywork and manufacturers look to exclude unnecessary materials that can release dust, fibres, and other particles, in these locations. Belts are used in many paint rooms on installations that move the car bodies into and out of the spray booths. This process is performed before mounting the car assembly with tires. A Volta fabrication was selected to carry bodies with no risk of marking the frames or of shedding fibres on contact points of the heavy workpieces.
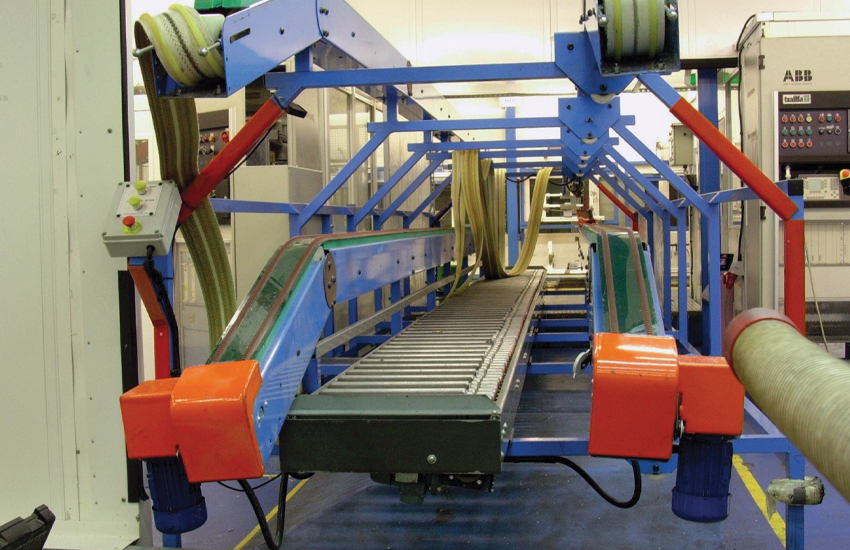