Home » Industries » Food & Hygiene » Meat
Meat
Meat processing kill plants convey heavy products past workstations such as deboning and jointing lines. Conveyors need to have strength and exceptional hygiene. Hygiene in meat processing can come at a cost with auditing standards demanding frequent washdowns and disinfections. Our product consistently tests with lower bacteria levels than conventional belts. The reduction of water usage and manpower required to service, provides major savings. It has an environmental impact as well reducing water treatment costs which make Volta thermoplastic conveyor belts a safe and economic choice. We supply full slaughterhouse lines including cleated belt elevators for frozen meat.
Stainless Steel belt retrofit
Stainless steel boning and trimming belts with a non-food grade black rubber V-guides are still in use in the meat industry. These guides produce a black powder that eventually migrates to the surface requiring intermittent costly wash downs. They also require periodic replacement which is a difficult and expensive repair. The challenge in retrofitting, is mainly in providing a stable belt that can run on the very large set of pulleys at either end such as a diameter of 700mm. In order to maintain width rigidity, the belt selected was a 4mm thick H material. The H material is the hardest of our flat belt options. Because of the sharp bones and knives in the working environment H material was the natural choice for the heavy jointing work performed on and around the belt. This material resists scratching and is impervious to fats and fluids released by the portions. The 4mm version was chosen for its ability to hold the wrap around the narrow-gauge wheel pulleys without lateral deformation. Food grade guides were welded on the base in place of the fast-wearing degrading rubber guides which drive and track the belt.

Offal/Organ containment
A newly equipped pork abattoir commissioned a set of conveyors designed with two flat belts that transferred offal at 90 degrees on a corner. The belts used synchronized compartments comprising of full width cleats, to keep each set of organs separate until the veterinary service on site had confirmed the meat as fit for consumption. The original design called for the belts to run through a hot water bath on the return to clean off possible pathogens that would contaminate the next load. After trials, it was clearly demonstrated not only that the system prevented leakages from each compartment onto the belt, but that cold water was enough to render the Volta SuperDrive™ belts ‘fit for use’ thus saving the energy required to heat the water and making the working environment safer. The factory equipped all its conveyors with Volta M material and saved on water and chemical consumption and labor required to clean. Similar options are made for beef abattoirs where closed compartments can be fabricated onto the base belt – this option gives a closed structure on all four sides and can be made in any length of width needed to accommodate different expected loads.
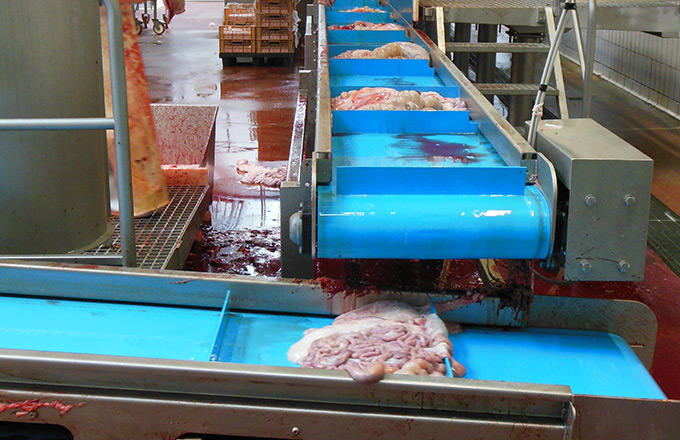
Retrofit from inferior thermoplastic belt
Not all thermoplastic belts are equal. Our partners were called to an abattoir where a 1” pitch belt similar in style to Volta Mini DualDrive™, had failed on a long jointing line. The belt was found to be unsuitable to the demands of the work required. The belt was elongating under the load and was off-tracking continually due to the side-loading force from the workstations. A Volta Mini DualDrive™ belt was fitted with no changes to the conveyor. The belt was shortened to eliminate problematic and unsafe catenary sag and a clever off-tracking prevention was added. The belt has worked trouble free since 2019 and has better cleanability as a bonus.
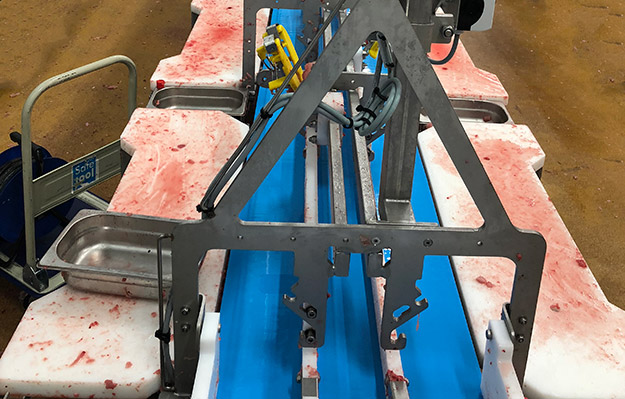
Frozen meat blocks elevator
A well-known producer and seller of meat patties used modular belts for the elevation of 25kg frozen blocks into a grinder at an angle of about 85 degrees. The loading is manual and relies on workers paying close attention to the exact position of the moving belt. Mistakes in the delivery coordination can trap a frozen block and break the cleat, introducing plastic into the grinder forcing recalls. This also makes the cleat unusable reducing output on the belt, even rendering the belt unusable until repaired or replaced. The Volta workshop welded 4 gussets onto each cleat for support for a perfect result.
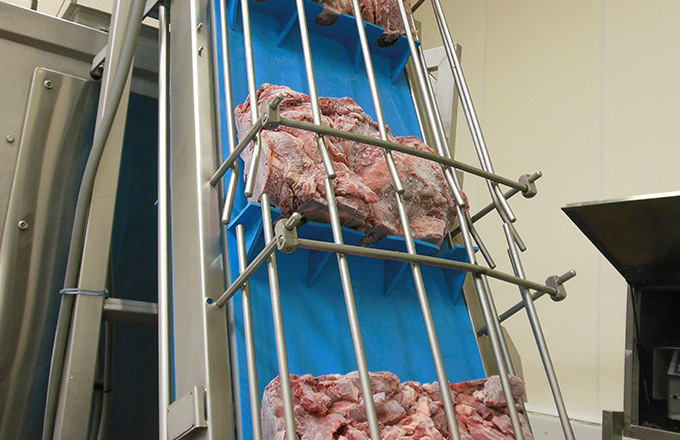